Maintaining high quality standards is a key part of Vision Technologies’ ethos. Over the years, Vision Technologies’ quick ascension to one of the largest sports manufacturers from Pakistan can be attributed to the increased demand from customers which stemmed from Vision Technologies’ ability to meet international quality standards. Understanding the quality is not a one investment, Vision Technologies continues to reinvest in its quality standards to meet and exceed international standards. Over the years, modernizations efforts continue to transform Vision Technologies into a Lean Manufacturing organization and building upon the Toyota Production System to continuously improve our quality standards that not only meet but also exceed the requirements of our customers.
Awards
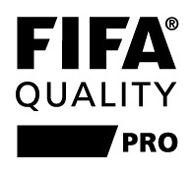
FIFA Quality Pro
ISO (the International Organization for Standardization) is a worldwide federation of national standards bodies (ISO member bodies). The work of preparing International Standards is normally carried out through ISO technical committees. Each member body interested in a subject for which a technical committee has been established has the right to be represented on that committee. International organizations, governmental and non-governmental, in liaison with ISO, also take part in the work. ISO collaborates closely with the International Electrotechnical Commission (IEC) on all matters of electrotechnical standardization.
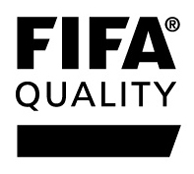
FIFA Quality
ISO (the International Organization for Standardization) is a worldwide federation of national standards bodies (ISO member bodies). The work of preparing International Standards is normally carried out through ISO technical committees. Each member body interested in a subject for which a technical committee has been established has the right to be represented on that committee. International organizations, governmental and non-governmental, in liaison with ISO, also take part in the work. ISO collaborates closely with the International Electrotechnical Commission (IEC) on all matters of electrotechnical standardization.
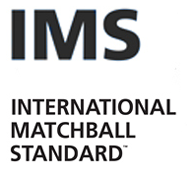
Internation Matchball Standard
ISO (the International Organization for Standardization) is a worldwide federation of national standards bodies (ISO member bodies). The work of preparing International Standards is normally carried out through ISO technical committees. Each member body interested in a subject for which a technical committee has been established has the right to be represented on that committee. International organizations, governmental and non-governmental, in liaison with ISO, also take part in the work. ISO collaborates closely with the International Electrotechnical Commission (IEC) on all matters of electrotechnical standardization.
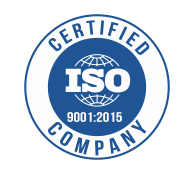
ISO 9001-2015
ISO (the International Organization for Standardization) is a worldwide federation of national standards bodies (ISO member bodies). The work of preparing International Standards is normally carried out through ISO technical committees. Each member body interested in a subject for which a technical committee has been established has the right to be represented on that committee. International organizations, governmental and non-governmental, in liaison with ISO, also take part in the work. ISO collaborates closely with the International Electrotechnical Commission (IEC) on all matters of electrotechnical standardization.
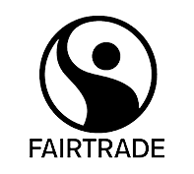
FairTrade
ISO (the International Organization for Standardization) is a worldwide federation of national standards bodies (ISO member bodies). The work of preparing International Standards is normally carried out through ISO technical committees. Each member body interested in a subject for which a technical committee has been established has the right to be represented on that committee. International organizations, governmental and non-governmental, in liaison with ISO, also take part in the work. ISO collaborates closely with the International Electrotechnical Commission (IEC) on all matters of electrotechnical standardization.

BSCI
The Business Social Compliance Initiative (BSCI) is a leading supply chain management system that supports companies to drive social compliance and improvements within the factories and farms in their global supply chains. BSCI implements the principle international labour standards protecting workers’ rights such as International Labor Organization (ILO) conventions and declarations, the United Nations (UN) Guiding Principles on Business and Human Rights and guidelines for multinational enterprises of the Organization for Economic Co-operation and Development (OECD).
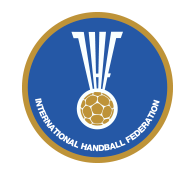
International Handball Federation
The International Handball Federation is the administrative and controlling body for handball and beach handball.
Certifications
ISO
9001
Quality Management
ISO 9001
Quality Management
ISO (the International Organization for Standardization) is a worldwide federation of national standards bodies (ISO member bodies). The work of preparing International Standards is normally carried out through ISO technical committees. Each member body interested in a subject for which a technical committee has been established has the right to be represented on that committee. International organizations, governmental and non-governmental, in liaison with ISO, also take part in the work. ISO collaborates closely with the International Electrotechnical Commission (IEC) on all matters of electrotechnical standardization.
ISO
14001
Environmental Management
ISO 14001
Environmental Management
ISO (the International Organization for Standardization) is a worldwide federation of national standards bodies (ISO member bodies). The work of preparing International Standards is normally carried out through ISO technical committees. Each member body interested in a subject for which a technical committee has been established has the right to be represented on that committee. International organizations, governmental and non-governmental, in liaison with ISO, also take part in the work. ISO collaborates closely with the International Electrotechnical Commission (IEC) on all matters of electrotechnical standardization.
SA
8000
Social Accountability
SA 8000
Social Accountability
ISO (the International Organization for Standardization) is a worldwide federation of national standards bodies (ISO member bodies). The work of preparing International Standards is normally carried out through ISO technical committees. Each member body interested in a subject for which a technical committee has been established has the right to be represented on that committee. International organizations, governmental and non-governmental, in liaison with ISO, also take part in the work. ISO collaborates closely with the International Electrotechnical Commission (IEC) on all matters of electrotechnical standardization.
OHSAS
18001
Occupational Health & Safety Management
OHSAS 18001
Occupational Health & Safety Management
ISO (the International Organization for Standardization) is a worldwide federation of national standards bodies (ISO member bodies). The work of preparing International Standards is normally carried out through ISO technical committees. Each member body interested in a subject for which a technical committee has been established has the right to be represented on that committee. International organizations, governmental and non-governmental, in liaison with ISO, also take part in the work. ISO collaborates closely with the International Electrotechnical Commission (IEC) on all matters of electrotechnical standardization.
Process
Vision Technologies has a thorough quality control process to ensure adherence to quality standards. The process itself is dynamic, not static, and evolves overtime to allow for continuous improvement and superior products for Vision Technologies’ customers. Moreover, quality control measures exist throughout the production process to offer multi stage checks which helps to produce a superior end product for customers.
-
Casing Material
When the planning team conceives an idea of a product article, a suitable casing material is developed in the given range of the product. Some common casing materials include Polyurethane, TPU, PVC, among several others. After the appropriate casing material has been selected, a series of tests are conducted to ensure quality of the casing material.
- Physical properties: surface appearance, color shades, touch feelings, GSM, thickness
- Mechanical properties: tensile testing to check elongation which helps to achieve the appropriate shape of a ball
- Chemical testing: hydrolysis test with an Alkaline solution at a PH value between 13 ~ 15. This test ensures the life cycle of the product.
- Weather Testing: given Vision Technologies’ products are exported to different regions of the world, special equipment is used to perform tests for varying temperature, humidity levels, UV index.
- Abrasion Test
Backing Material
Different types of fabrics and foams are used based on required performance and class of the product. The following tests are performed to ensure quality of these materials, which ultimately show up in quality of the ball.
- Tensile testing
- Fabric composition testing: to check presence of cotton, polyester, viscos, and others
- Foams: thickness, density, softness, GSM
Bladder
Bladders play an important role in the performance of sports balls and as such are tested in detail.
- Water Testing: each bladder is dipped in water to check if there is any leakage in the bladder
- Physical checking for any damage on the shell or valve part of the bladder
- Bladders are then inflated and kept on hold for 24 hours to determine if there is any slow leakage in the bladder.
Once the materials have passed through these testing procedures, they are passed on to the product development department.
-
After quality has been approved in the material development process, the product development team conducts a series of steps on a finished product item.
- Knife cut: cutting tool determines the shape and look of the ball to ascertain whether or not it meets requirements
- Ink : ink formulation is set for graphics of the ball. As balls are played on different types of surfaces, a lot of abrasion occurs during play, this abrasion tests are performed through special equipment designed to test how the ink withstands abrasion.
- Shooter Test
- Bounce Test
- Water absorption Test
- Circumference Test
- Air Retention Test
- UV Test
- Weather Test
- Fungus Test: to check if everything is within quality standard.
After a product passes quality tests in the product development department, only then is an order released for production en masse. During mass production, the production team makes sure that all the parameters set by the development team are met during the production process and the ball is within the quality standard set for the particular product.
-
After receiving an order for mass production, additional processes exist to ensure quality in the entire chain of operations.
Material Quality Control : The Material QC team receives material for mass production and conducts their tests to ensure the articles are ready to be released. This team checks for:
- Thickness
- Weight (GSM)
- Color shade
- Backing cloth
- Density (in case of foams)
-
There are two types of laminations that are performed at Vision Technologies: manual lamination and machine lamination. During the lamination process, the material is tested for weight, adhesion strength and humidity.
- Weight: The weight of the material is controlled to make sure that the final product is within the required standard.
- Adhesion Strength: Adhesions tests are performed to ensure the bonding strength of the lamination between different layers so as to ascertain that materials are strong enough to handle playing conditions.
- Humidity: Humidity level of each sheet / roll is checked to avoid development of fungus on the material. Antifungal chemicals are added in the adhesive to make sure that fungus does not grow if the final product is used in a humid or warm weather
-
Automatic cutting presses are installed in this department to ensure proper cutting of panels and to minimize human error. Each production order has a corresponding work order that is generated by the production office. The work order mentions the appropriate cutting to be used on any particular work order.
Cutting tools are properly stored with their corresponding labels so that the incorrect tools are not used in the production process for a particular order. -
After the laminated sheets have been gone through panel cutting, they move over to the printing department. Along with the cut panels, the printing team is provided with the approved artwork and an approved sample ball for the corresponding work order.
Ink shades are mixed and checked by Konica Spectrometer, to ensure correct color is printed. A few balls are printed as pre-production samples which are then subject to the approval of the QC inspector. Once the QC inspector gives his/her green signal, printing on the order starts.
Once the printing is in process, a QC inspector performs random checks to ensure that there aren’t any issues in the quality of the printing on the panels. After a batch order has been completed, a QC inspector performs an inspection on an AQL basis. If the batch order is within set standards, it is passed on to the next department: panel sorting. -
After the printing process, panels are moved to a sorting department where a team sorts panels according to the complete final product configuration while also looking for any faults on the panel such as
- Color variation
- Incorrect design
- Missing or additional panels
The panels are then batched together and sent to the stitching department.
-
After the sorting department has sorted the panels and prepared panel kits, the panels move to the stitching department. Vision technologies performs two kinds of stitching: simple machine stitching and hybrid.
- Simple machine stitching requires panels to be stitched together to create a casing for balls. QC inspectors monitor the process and keep a lookout for:
- Correct number of stitches being applied
- Stitches applied at correct location
- Alignment of the design among different panels
- Placement of every panel at the correct location
- Machine setting is as per recommendation
Once the casing is completed, the bladder is attached with the casing. The QC inspector randomly checks that bladders are properly bonded with the casing of the ball.
- For the hybrid ball, after the casing is completed (in the same way as the machine stitching process), Vision Technologies bonds foam with each panel of the ball. The QC team checks if these foam panels are properly bonded with the casing panels.
- Simple machine stitching requires panels to be stitched together to create a casing for balls. QC inspectors monitor the process and keep a lookout for:
-
During the stitching process, an in-line QC inspector is responsible for making sure that products are properly stitched. Once the products have been stitched, there is a second layer of quality control to check products at the end-of-the-line.
The job of this QC team is to check that products were properly stitched, there are no uneven panels, stitching is not loose, all panels are stitched at their proper location, and products are properly cleaned so that they are ready for packing.
For balls, they are inflated and put on hold for 24 hours to check if there is any leakage in them. After 24 hours, a QC inspector checks the air pressure in each ball with a digital air pressure gauge. All the balls which have air pressure within the set standard are passed over to the packing department, which as a precautionary method, again physically checks the balls before packing them in the boxes. -
Before orders are sent out for shipping, they are stored at the warehouse. While orders wait at the warehouse, QC inspectors randomly inspect products from the ready-to-be-shipped cargo to perform QC checks.